Custom Metal Stamping Services
Custom metal stamping with fast turnaround and tight tolerances — ideal for low- to high-volume production in automotive, electronics, and industrial applications.
- Stamping thicknesses from 0.2 mm to 6 mm
- ±0.05 mm stamping accuracy for consistent quality
- Supports low-volume and high-volume runs up to 100,000+
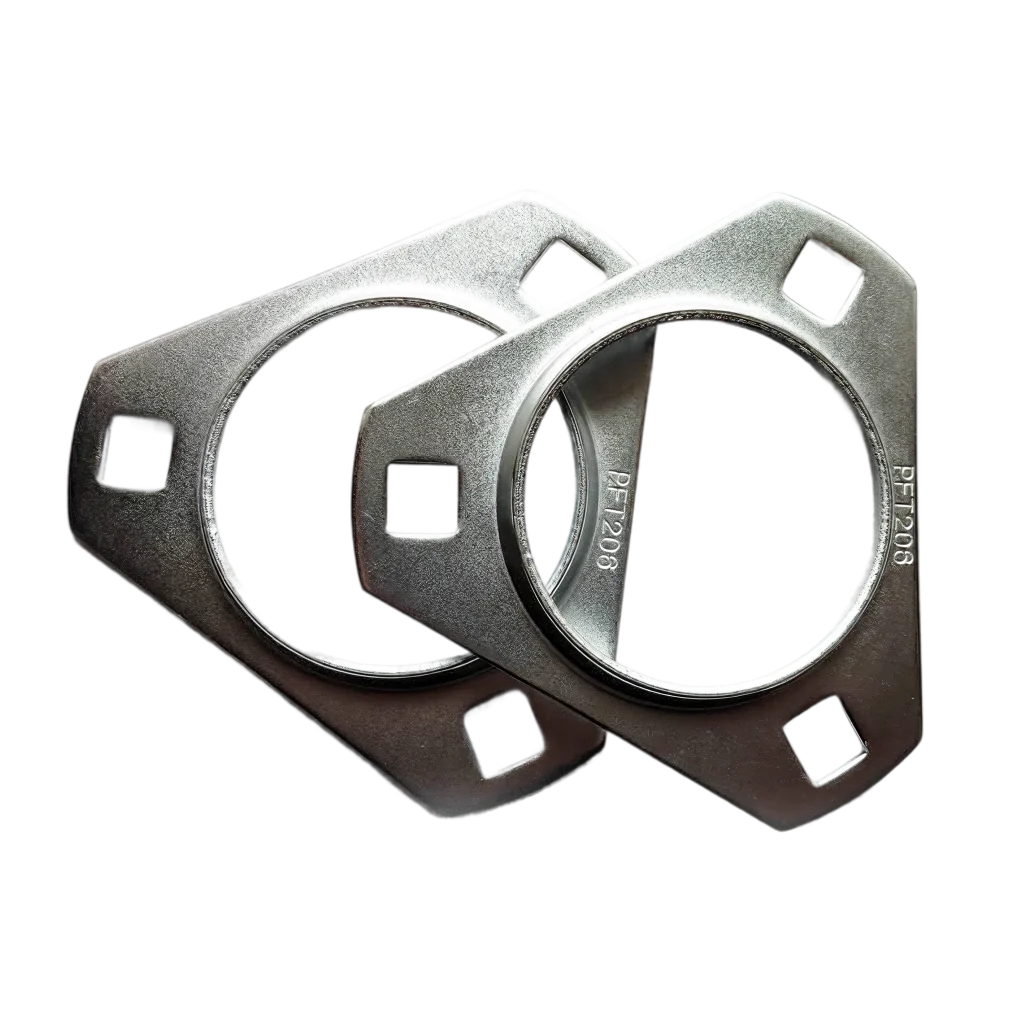
How Our Metal Stamping Process Works
Our metal stamping process is built for precision and speed—from tooling to final inspection, every step ensures consistent quality.
Metal Stamping Parts Gallery
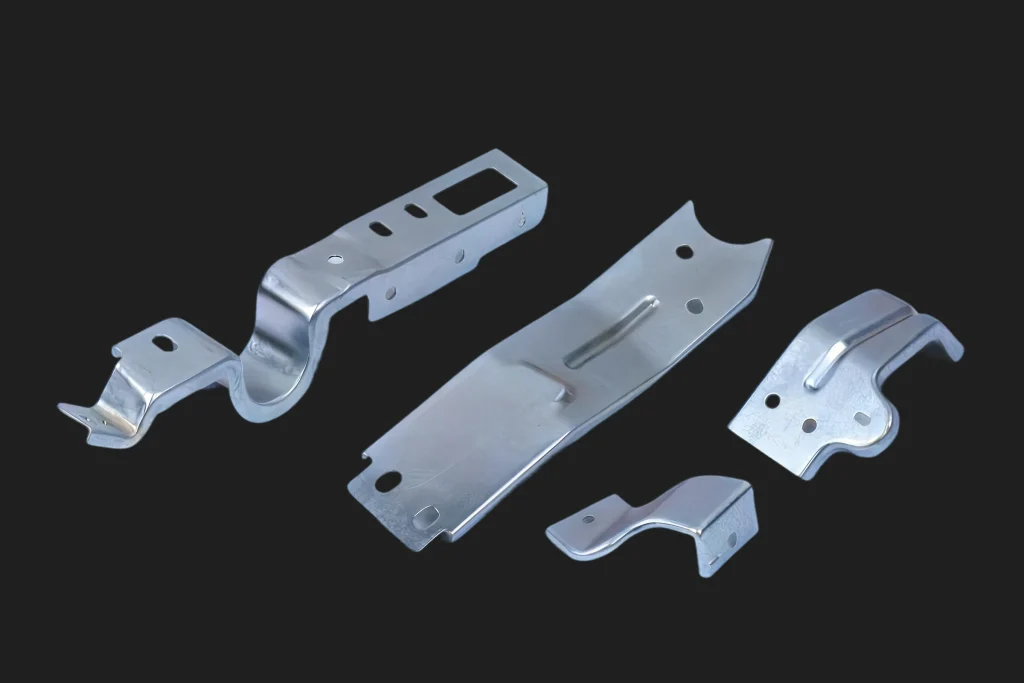
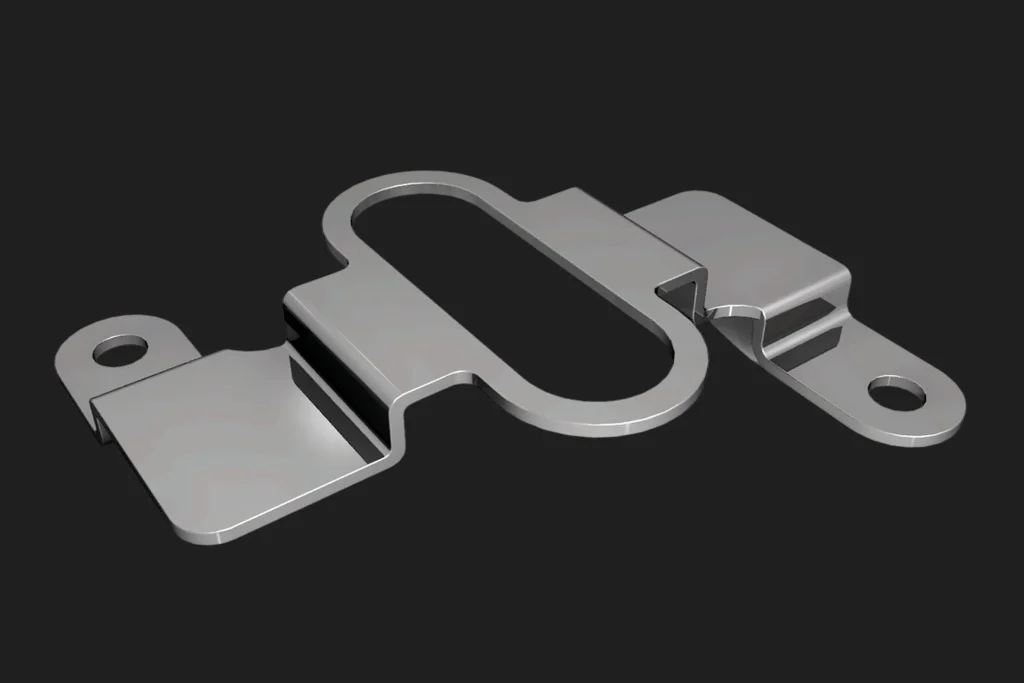
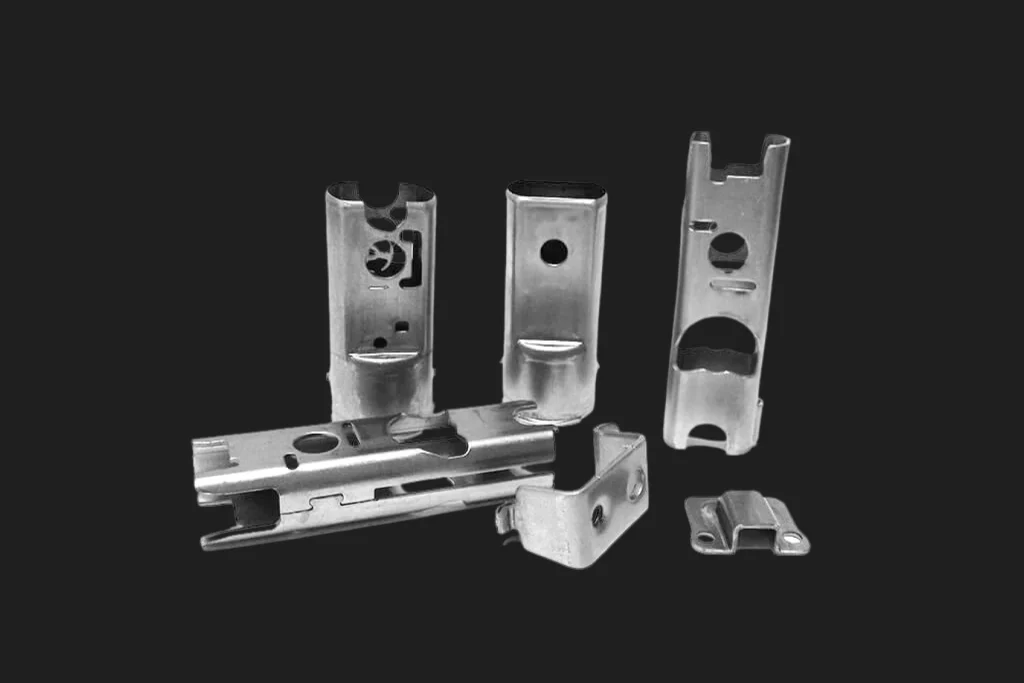
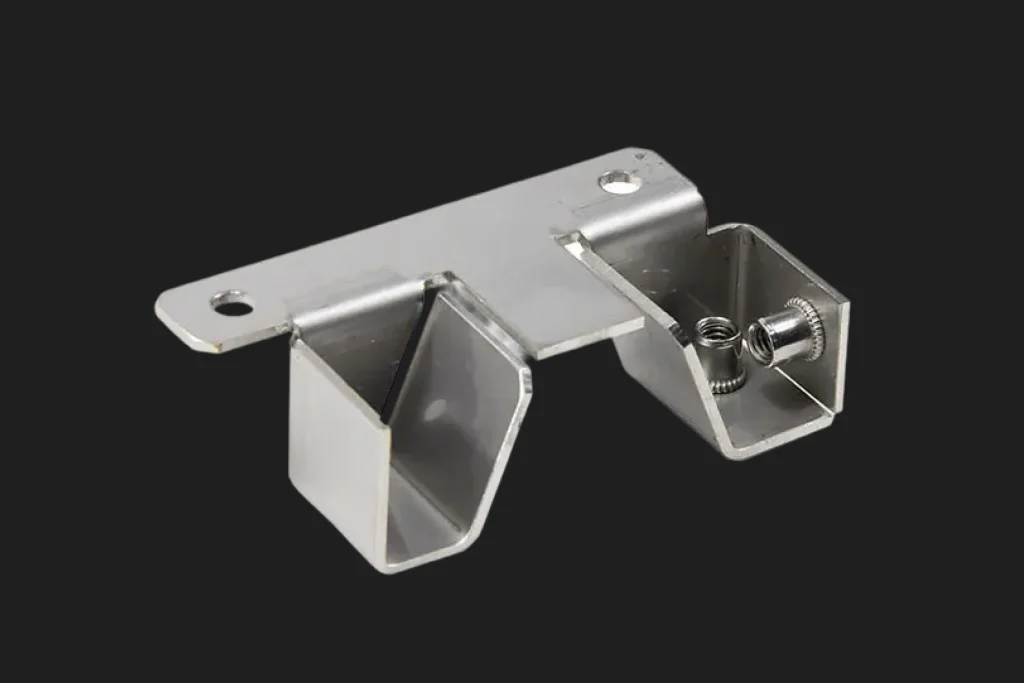
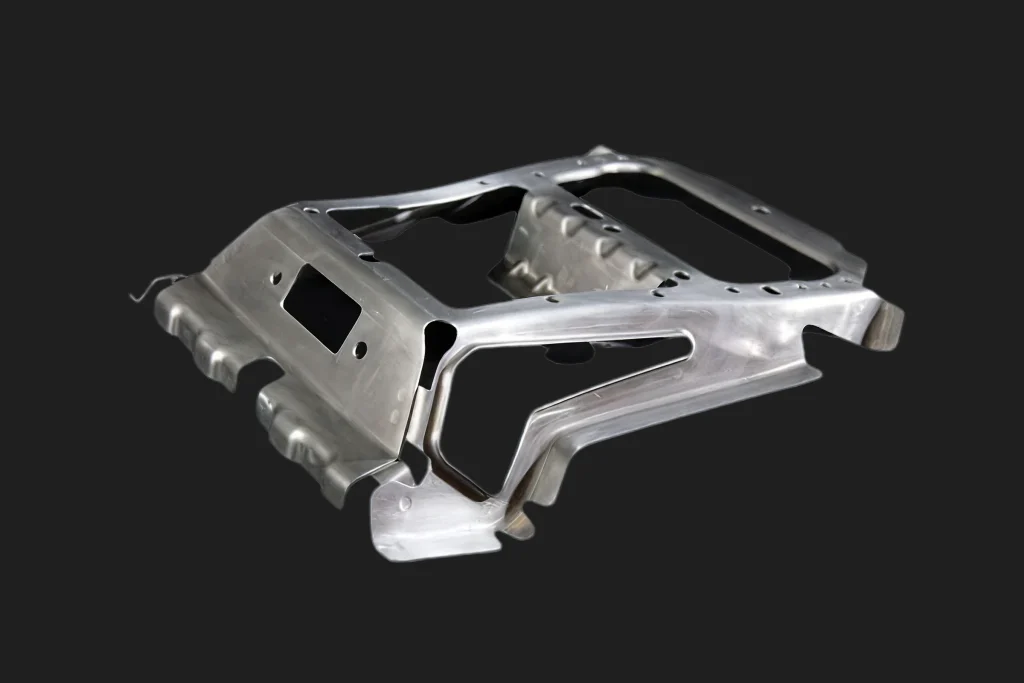
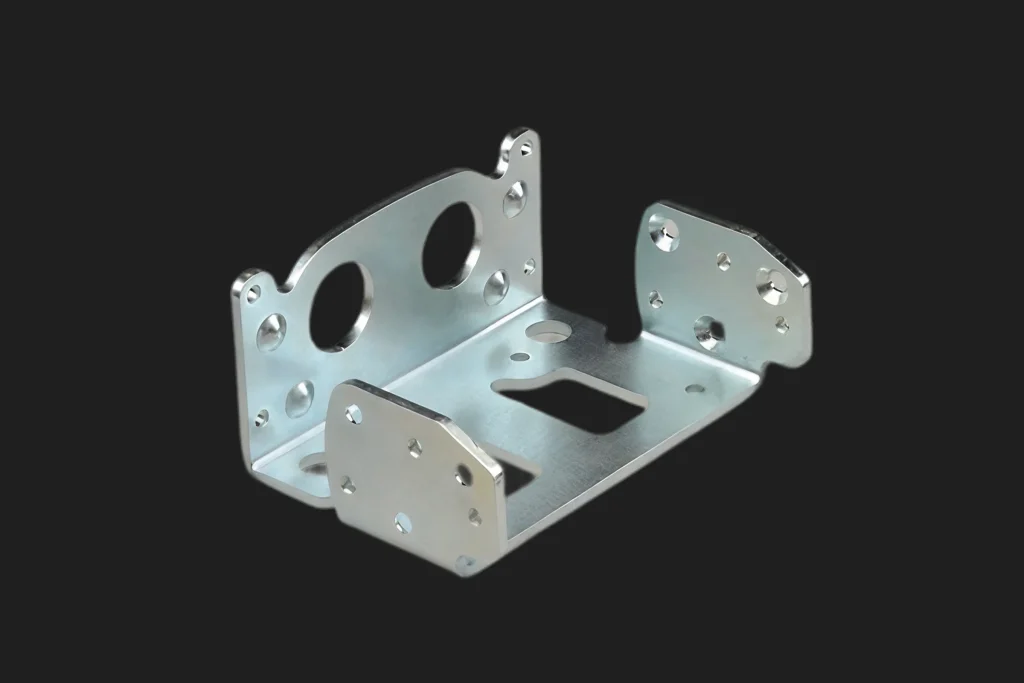
Why Choose LTC as Your Metal Stamping Partner
Tight tolerances ensure consistent, high-quality parts every time.
Stamping available in stainless steel, aluminum, copper, and more.
Streamlined processes for quick turnaround on all order sizes.
From prototyping to millions of parts—no volume is too small or large.
LTC Proto's Types of Stamping
We provide single-stage, multi-stage, progressive die, deep draw, and fourslide stamping to suit different production needs. LTC Proto’s team reviews your 3D models and drawings to recommend the most suitable method for your parts.
Types | Description |
---|---|
Progressive Die Stamping | Progressive die stamping forms complex, deep parts in multiple steps—ideal for high-volume production. Transfer die moves parts individually, not on a continuous strip. |
Deep Draw Stamping | Deep draw stamping forms rigid, deep-cavity parts by heavily deforming metal. Standard draw stamping uses shallower dies for less complex shapes. |
Fourslide Stamping | Fourslide stamping forms parts from four sides, ideal for small, complex components. It's fast, flexible, and cost-effective for electronics, medical, and aerospace industries. |
Hydroforming | Hydroforming uses high-pressure fluid to press metal sheets into die shapes—fast, precise, and ideal for forming multiple parts at once. |
Blanking | Blanking cuts raw shapes from sheet metal; fineblanking offers smoother edges and higher precision for tight-tolerance parts. |
Coining | Coining forms small round parts with high force, hardening the metal and eliminating burrs and rough edges. |
Punching | Punching removes material from a workpiece, unlike blanking, which cuts out a piece to form a part. |
Embossing | Embossing forms 3D designs in metal, creating raised patterns or depressions on the surface. |
Bending | Bending shapes metal along one axis into U, V, or L forms, while flanging creates tabs by bending specific workpiece areas. |
Note: This table outlines general tolerances for LTC Proto sheet metal services. Contact us for more details on our fabrication standards.
Find the Right Stamping Method
Not sure which stamping process suits your part? Talk to our engineers for expert guidance and recommendations.
Metal Stamping Materials
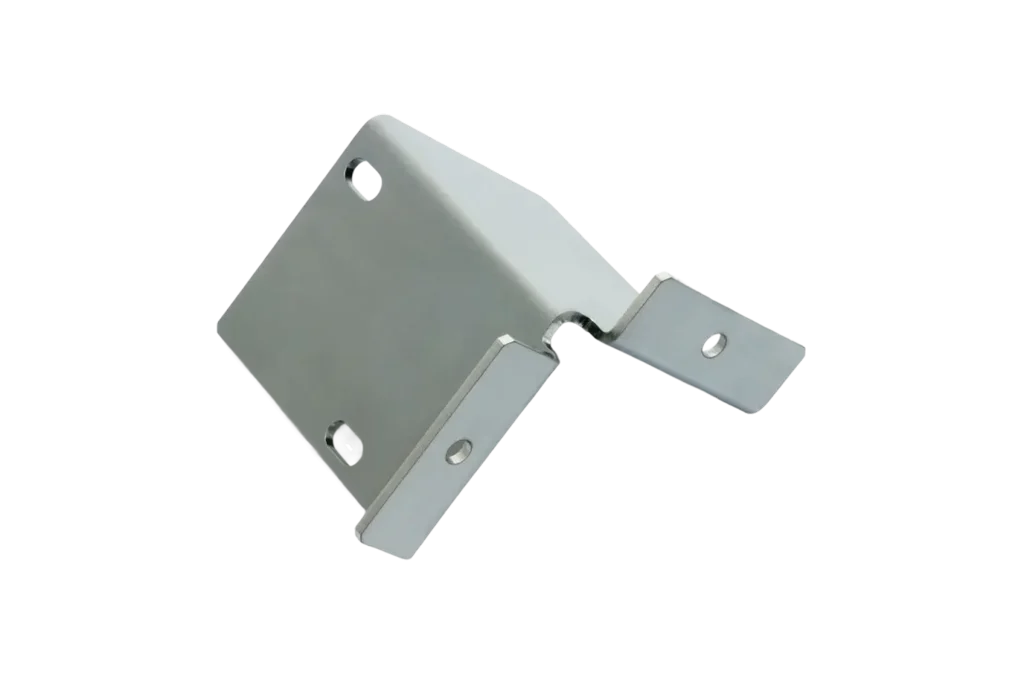
Steel
Cold rolled steel is a popular choice for stamping due to its formability and strength. Common grades include:
1008
1010
1018
These general-purpose materials are ideal for cold forming applications.
Price: $$$
Lead Time: 7 business days
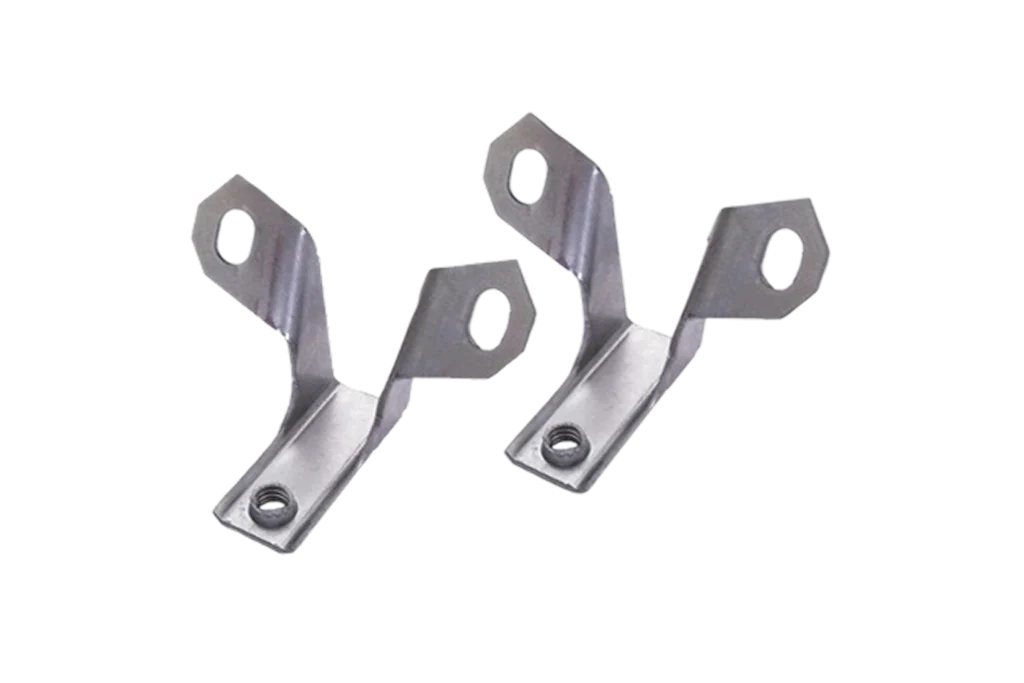
Stainless Steel
Stainless steel is widely used for its durability and resistance to corrosion, especially in high-temperature environments. Common grades include: construction.
301
304
316/316L
Price: $$$
Lead Time: 7 business days
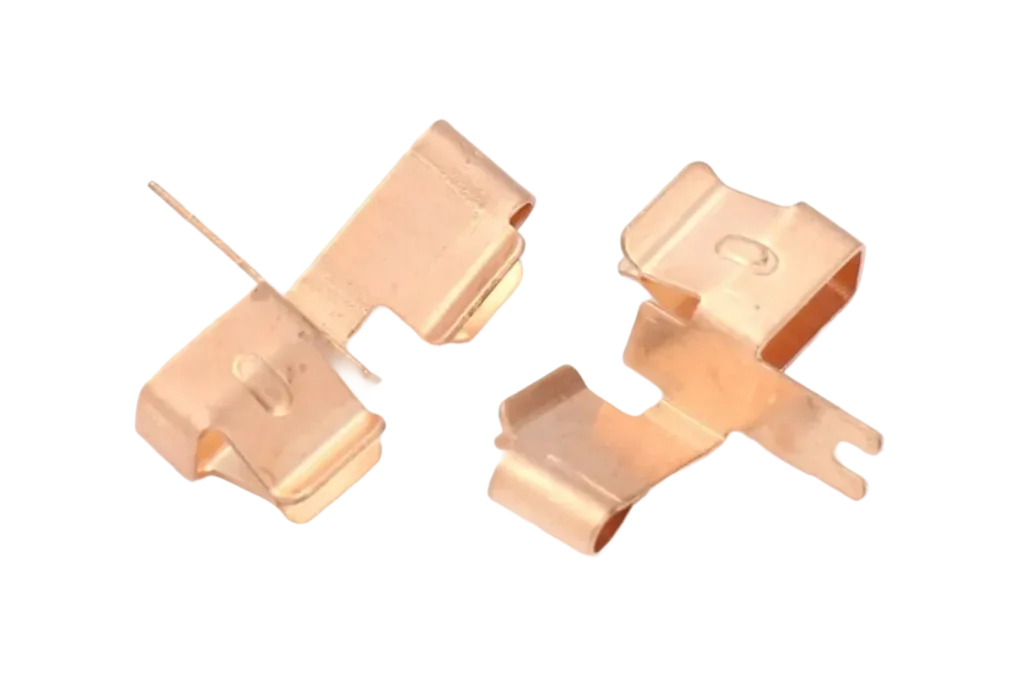
Copper
Copper is known for its excellent conductivity and ease of forming. Common grades include:
- C110
This grade is ideal for applications requiring high conductivity and good forming properties.
Price: $$$
Lead Time: 5 business days
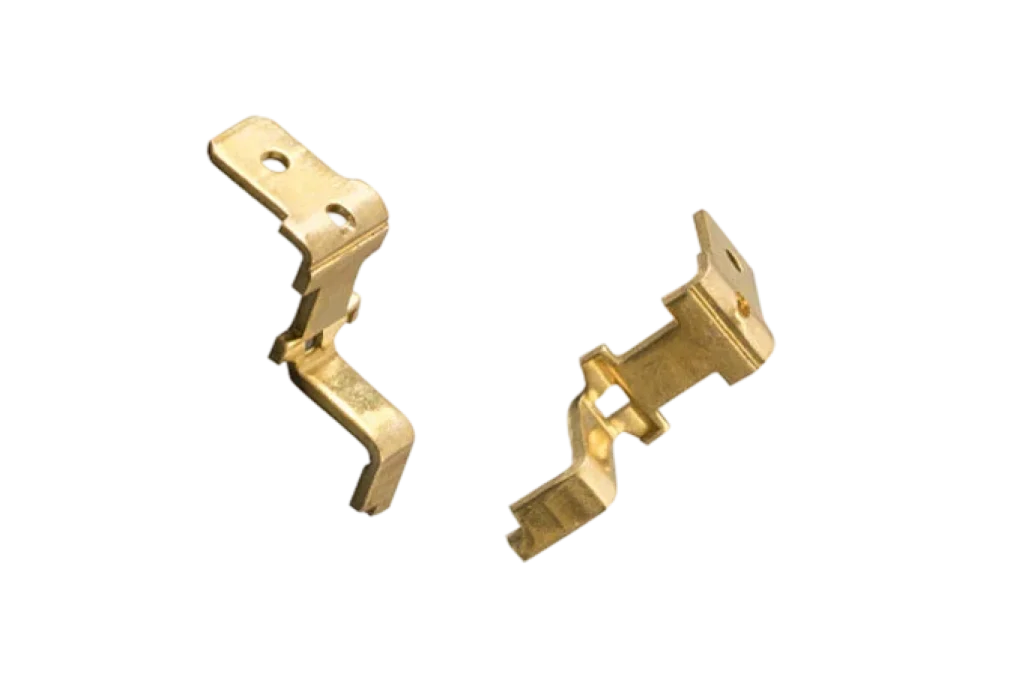
Brass
Brass alloys are highly formable and resistant to corrosion. Common grades include:
230 (85/15) – Red Brass
260 (70/30) – Yellow Brass
These alloys are known for their excellent machinability and durability in various applications.
Price: $$$
Lead Time: 5 business days
Note: The above table only shows some common materials. We have more than 20 materials for you to choose from. Please feel free to contact us for confirmation!
Metal Stamping Production Volumes
At LTC Proto, we tailor each production volume option to meet the specific needs of your project, ensuring high-quality results, cost-efficiency, and on-time delivery.
Low volume production refers to quantities up to 100,000 units. Most stamping projects start at 1,000 units to ensure cost-effectiveness. It’s ideal for bridging the gap between prototypes and mass production, or testing market demand. It also supports custom product requests. LTC Proto offers competitive per-unit pricing, even for small runs.
Medium volume production ranges from 100,000 to 1 million units. It combines the flexibility of low-volume runs with reduced per-part costs and lower upfront tooling expenses.
Short-run stamping involves low-volume production with minimal tool changes, keeping costs low. Very short runs have no process changes, offering the lowest prices. Ideal for parts with low volume or market entry.
High volume production involves orders exceeding 1 million parts. Metal stamping is highly scalable and cost-effective for large runs, reducing unit costs by spreading custom tooling expenses across many parts.
Long-run stamping is a comprehensive production process with variable factors, offering flexibility as the production line is optimized for scale. While it involves higher costs due to testing and adjustments, it ensures consistent quality, low per-unit costs, and high throughput—up to hundreds of parts per minute.
Our Tight Tolerances and Quality Assurance
Our suppliers optimize tool and die designs to meet strict tolerance requirements, ensuring precise outcomes. However, tighter tolerances can increase both complexity and cost.
Routine inspections ensure that output meets specifications, supported by a Total Productive Maintenance (TPM) program for consistent quality. Stamping tools are regularly checked for wear, and check-fixtures or check-gauges are used for long-run stamping lines.
Metal Stamping Parts Applications
Automotive
Metal stamping produces durable parts like brackets and panels, meeting strict safety and performance standards.
Aerospace
Used for lightweight, strong components like panels and engine parts, ensuring precision and reliability for safety.
Medical Devices
Essential for high-precision parts like surgical tools and implants, with strict adherence to safety and regulatory standards.
Consumer Electronics
Manufactures parts like connectors and casings for devices, requiring durability and precise fit.
Telecommunications
Produces components such as connectors and frames, supporting high-speed data transmission and durability.
Industrial Equipment
Creates durable parts like gears and brackets, designed to withstand heavy loads and harsh environments.
Robotics
Used for parts like enclosures and joints, requiring precision for reliable operation.
Defense and Military
Critical for creating strong, reliable parts for weapons and equipment, meeting high standards for safety and performance.
Advantages and Disadvantages of Metal Stamping
Pros of Metal Stamping
Stamping is ideal for producing complex parts at scale. It specifically offers:
- Delivers low cost per part for mass production
- Capable of producing intricate shapes and contours
- Suitable for thick sheet metals using processes like fineblanking
- Scalable for high-volume production—thousands to millions annually
Cons of Metal Stamping
Metal stamping comes with upfront tooling costs and longer setup times. Once the tooling is complete, production becomes fast and cost-effective. Key drawbacks include:
- Longer lead times for initial parts due to die fabrication time
- High upfront costs from tooling, check fixtures, and one-time engineering efforts
- Multiple die iterations may be required to ensure consistent, spec-accurate production
Get Stamped Parts Fast
Upload your 3D files now—LTC Proto delivers precise stamped parts with short lead times and competitive pricing.
Latest Blog
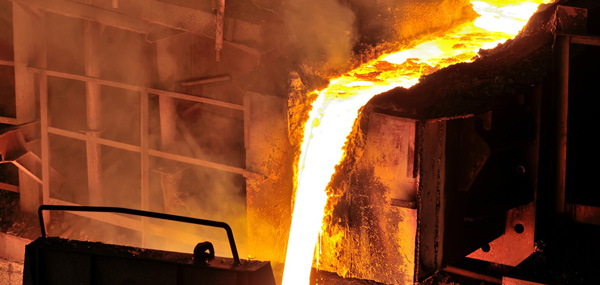
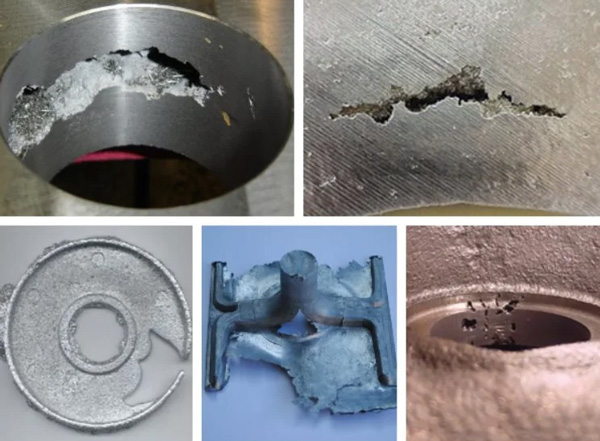